WOODSHOP NEWS Issue May 2020 – Barth Vacuum Press
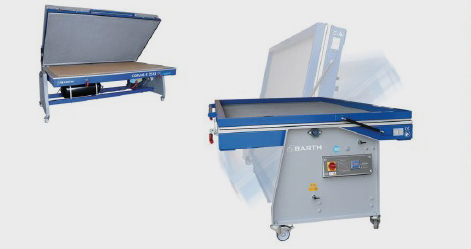
Bringing thermofoil in-house is a viable option for many small- to medium-sized woodshops because of advances in the technology, both in terms of machines and patterns. Foil makers are constantly introducing new solid colors and woodgrains, and the machines are getting small, more powerful and more efficient.
The theory is relatively simple. The shop mills one-piece flat or panel MDF doors on a CNC, and then wraps the backs first and then the fronts with vinyl in a heated, vacuum packing machine. The doors and drawer fronts are laid out on the bed of the machine, often with sophisticated platens that raise them off the surface or make it easier for woodworkers to apply or handle the hotmelt adhesive used to create a bond between the foil and wood products. After baking, the parts are trimmed from the sheet and turned over and the process is repeated for the front faces. The vacuum and heat suck the foil tight to the door profile, revealing flat or raised panels or details such as arched tops.
The advantages of thermofoil are that the material can be significantly less expensive, and the process is less labor-intensive than more traditional assembly and coatings options. One or two workers can turn out a full set of doors and fronts in a day, and there’s no overnight eure or multiple coating required.
The biggest disadvantage is that thermofoil is shaped by heat, and usually lies on an MDF core. The foil is susceptible to heat after installation such as hair dryers, coffee machines and toasters, and if the seal deteriorates the MDF core may absorb moisture and become distorted or swollen. lt can also meet some client opposition as there is a conception that these doors are a low-end solution for a high-priced custom job.
Other concerns are handling vinyl with preapplied glue, dust or dirt that telegraphs through the vinyl, and delamination. Sometimes, the doors can be repaired with contact adhesive, but the normal solution is replecement. And that can be a problem if the vinyl pattern or color has been changed or discontinued, or if the tone or shade of adjacent doors and fronts has reacted to an environmental influence such as direct sunlight or cleaning chemicals.
But overall, thermofoil doors can really simplify life in the cabinet shop while offering the customer a solid value.
Options
Vac-U-Clamp (vacuclamp.com) in Oceenside, Calif. offers the FT 900 thermofoil vacuum press that can handle work up to 52″ x 105″ and it has a low-profile top that decreases the interior volume. That delivers optimum heat distribution, while shortening the cycling time. The machine has 24,000 watts of heating power, which is delivered through infrared quartz tubes. The top tubes are curved to more evenly distribute heat. And there’s a tube at each end for complete, even heating of the film. The temperature of the film is accurately measured by an infrared sensor, and there’s a centrally located 300-watt interior light so the operator can visually check progress through the front viewing window.
In a Vac-U-Clamp exclusive, optional platens are bonded with a very high-tech nonstick coating that prevents pre-glued film from sticking to the platens during processing. That makes removal of excess film a snap. Previously, shops that wanted to use pre-glued film had to spray the pletens with a food-type nonstick spray- which worked but was a mess and reguired frequent repeat applications. The new pletens can save a lot of set-up time between cycles and contribute to both a cleaner work environment and better results. Experienced users will also appreciate the Constant Row low level of vacuum, which helps eliminate wrinkles.